Large-scale productions of slush hydrogen and slush nitrogen
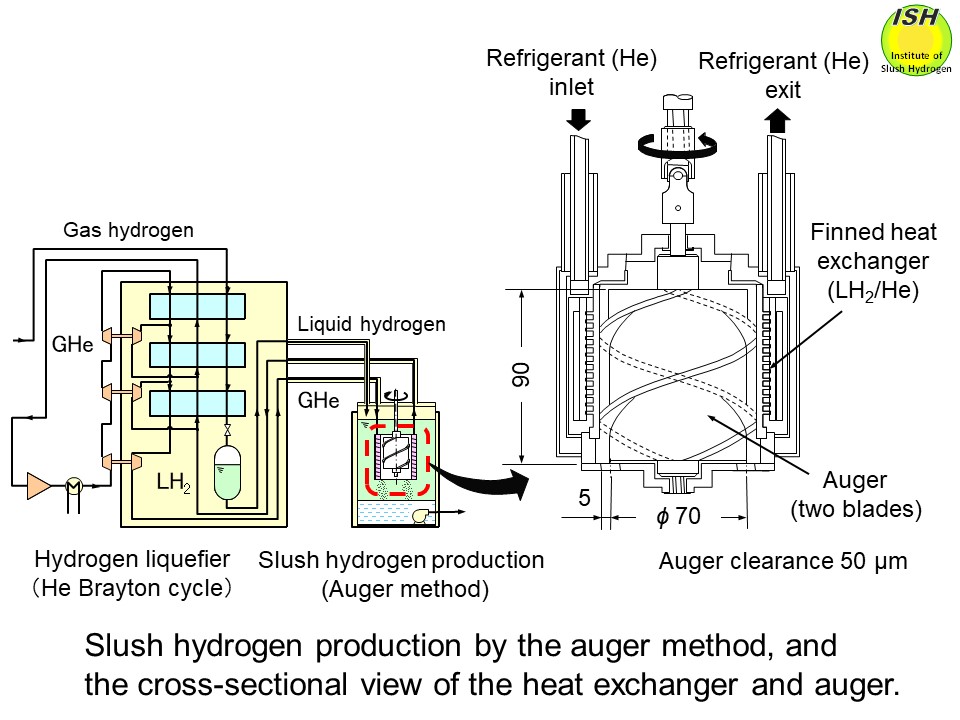
The major production methods of slush hydrogen are the spray, freeze-thaw,
and auger [6, 13, 14].
The spray method ➡ Inefficient production
In the spray method as shown in the photo below, a nozzle is used for the adiabatic expansion of high-pressure liquid
hydrogen to produce solid particles. However, most of liquid hydrogen evaporates during the expansion, and most particles
produced in this method melt down when mixed into liquid hydrogen, making
this method no practical use of not only the efficient large-scale production
but also the small-scale production for slush hydrogen and slush nitrogen.
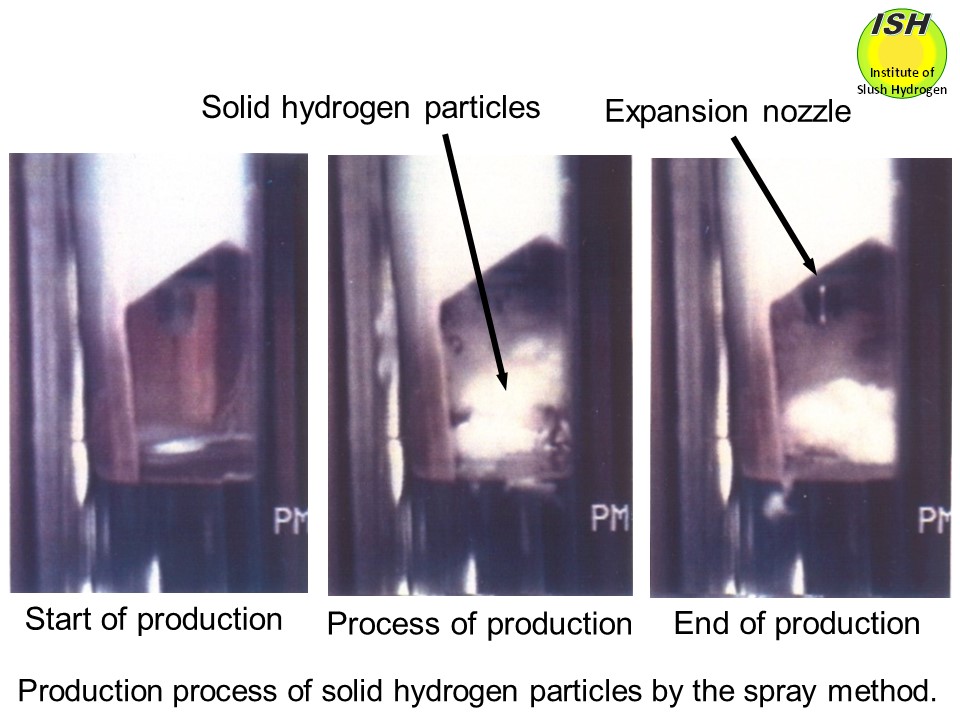
As an application of the spray method, the ejector method (two-fluid nozzle) has been proposed for the high-temperature superconducting (HTS) electrical power transmission. The ejector method uses a well-known but inefficient ejector effect of high-pressure cryogenic helium to produce solid nitrogen particles or slush nitrogen by the adiabatic expansion of liquid nitrogen in a nozzle.
In the production of solid particles, the ejector method uses an isenthalpic expansion process using a nozzle, whereas the auger method uses an isentropic expansion process using a helium gas turbine as shown in the figure at the beginning of this page. The isentropic process is much more efficient than the isenthalpic process in the temperature decrease of expansion gas.
The ejector method is inefficient and of no practical use in producing solid nitrogen particles or slush nitrogen as with the spray method.
Furthermore, flow and heat transfer tests using the produced slush nitrogen have not conducted at all, and the occurrence of pressure drop reduction in pipe flow, which is one of the important advantages for the use of slush fluid, is not yet verified by the experiments. The size of solid nitrogen particles produced by the ejector method, which is exaggeratedly called "microslush", is much smaller (submillimeter size of 0.1-0.3 mm, not micrometer size of 0.001mm) than that by the freeze-thaw method (around 1.36 mm as shown in the figure below), and the number of solid particles in slush nitrogen consequently increases at the same solid fraction. Since collisions occurring among the solid particles and between the solid particles and the pipe wall, and the drag force exerted by the liquid on the particles increase, the slush nitrogen suffers a notable loss of momentum, and the pressure drop thus increases. That is, there is a strong possibility that the pressure drop of the slush nitrogen flow with minute particles increases significantly compared to that of liquid nitrogen flow (no pressure drop reduction).
The ejector method also has some defects as follows: 1) the use of a large amount of high-pressure cryogenic helium (or liquid helium at the temperature of 4.2 K) causes the high cost of producing solid nitrogen particles or slush nitrogen, 2) it is difficult to recover helim from the mixed gas of helium and nitrogen, and at the point of conservation of scarce helium, this method is out of the question, 3) since helium dissolves in the produced slush nitrogen, helium bubbles are generated due to a slight increase in slush nitrogen temperature, and the quench or thermal runaway of superconducting equipments occurs due to decrease in the heat transfer performance of slush nitrogen as a refrigerant.
Therefore, the ejector method cannot be employed for the productions of slush nitrogen and slush hydrogen from the defects 1) and 2), and from the fatal defect 3), slush nitrogen and slush hydrogen produced by the ejector method cannot be used as a refrigerant for superconducting equipments.
The freeze-thaw method ➡ Small- to medium-scale production
The freeze-thaw method is a relatively straightforward method, and applicable at the experimental level or for small- to medium-scale production.
A vacuum pump is used for pressure reduction of liquid hydrogen at the
normal boiling point pressure. As the liquid boils and vaporizes in accordance
with the vapor-liquid equilibrium curve, the latent heat is removed and
the temperature of the liquid is reduced. When the liquid reaches the triple
point pressure, a frozen layer is formed on the liquid surface. When evacuation
is stopped, part of the frozen layer melts and solid hydrogen sinks into
the liquid. A stirrer is then used to break up the solid into small particles
having a diameter of several mm. Slush hydrogen is produced by performing
the freeze-thaw cycle repeatedly.
The slush hydrogen and slush nitrogen used for the experimental work are
produced using the freeze-thaw method. For slush nitrogen, particle sizes
in our experiments are in the range from 0.5 to 2 mm, with an average size
of 1.36 mm as shown in the figure below.
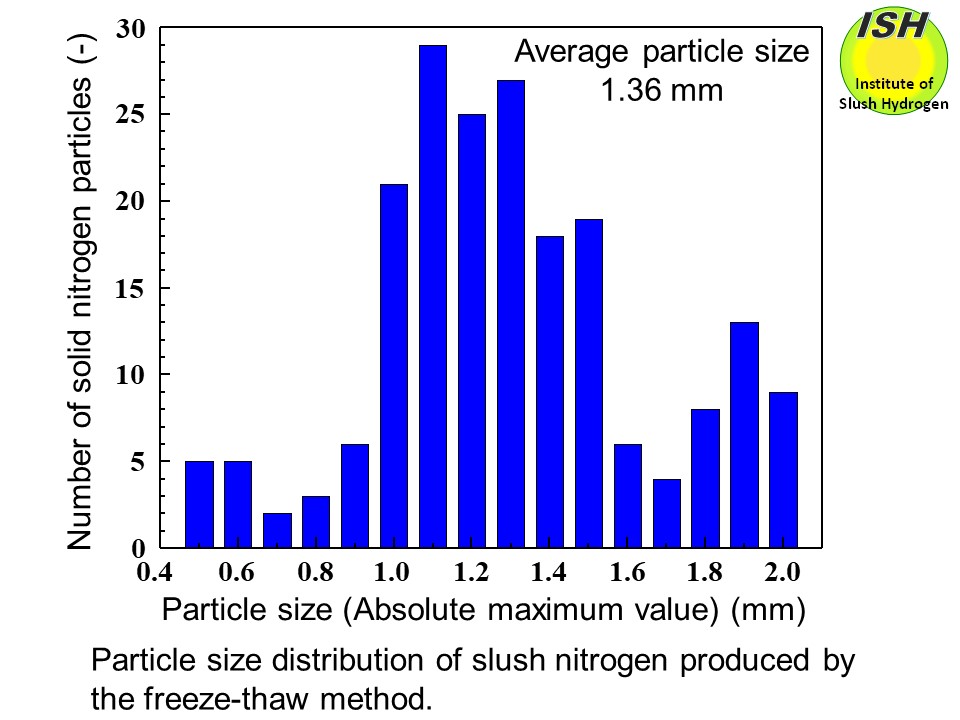
The auger method ➡ Large-scale production
In the auger method, as illustrated in the figure at the beginning of this page, solid hydrogen formed on the heat transfer surface due to heat exchange
between liquid hydrogen and lower-temperature gas helium is scraped off
by rotating blades known as an auger, to produce fine particles of solid
hydrogen. Since the heat exchanger and auger are immersed in the liquid
hydrogen, the solid hydrogen particles are mixed into the liquid during
the production process.
When cryogenic gas helium and liquid hydrogen are continuously supplied,
slush hydrogen can also be continuously produced, making this method suitable
for large-scale production. By adjusting the gap (clearance) between the auger and heat exchanger
surface and/or changing the rotational speed of the auger, the size of
solid particles can be controlled.
In our small-scale production experiments using the heat exchanger and
auger shown in the photo below with a visual observation at the auger speeds from 30 to 80 rpm, the solid
hydrogen production rate increases with speed, and the particle size becomes
smaller as shown in the photos below of 50 rpm and 80 rpm. The maximum solid production rate of 0.062 g/s is
obtained at an the auger speed of 80 rpm (two blades), equivalent to 5.5
l/h of slush hydrogen with a mass solid fraction of 50 wt.%.
The solid hydrogen production rate was calculated based on the heat transfer
model considering the auger speed and the growth of solid hydrogen thickness
(thermal resistance) on the heat transfer surface, and compared with the
test results. The calculated results for the auger speed and the solid
hydrogen production rate are shown in the figure below. The calculated results show that the production rate tends to rise with
the auger speed because of decrease in solid hydrogen thickness. Although
the heat transfer coefficient of helium is calculated to be approximately
1200 W/m2-K, comparing the experimental and calculated results, the heat transfer
coefficient is estimated approximately 700 W/m2-K. One reason why this is lower than the calculated value is thought to
be the clearance of 0.3 mm between the fin edges and the outer cylinder,
as shown in the figure at the beginning of this page, such that a part of helium flows upward through this gap.
At present, large-scale production experiments have yet to be carried
out. A combination of hydrogen liquefier using the helium Brayton cycle
and the auger method is already illustrated in the figure of “High-efficiency
hydrogen energy system using slush hydrogen”, resulting in the continuous
large-scale production of slush hydrogen.
To achieve practical application of the auger method for high-efficiency
large-scale production, improved performance of the heat exchanger and
long-term reliability of the auger mechanism rotating at cryogenic temperatures
are required. However, these technological problems can be solved with
almost no difficulty considering from the existing technologies.
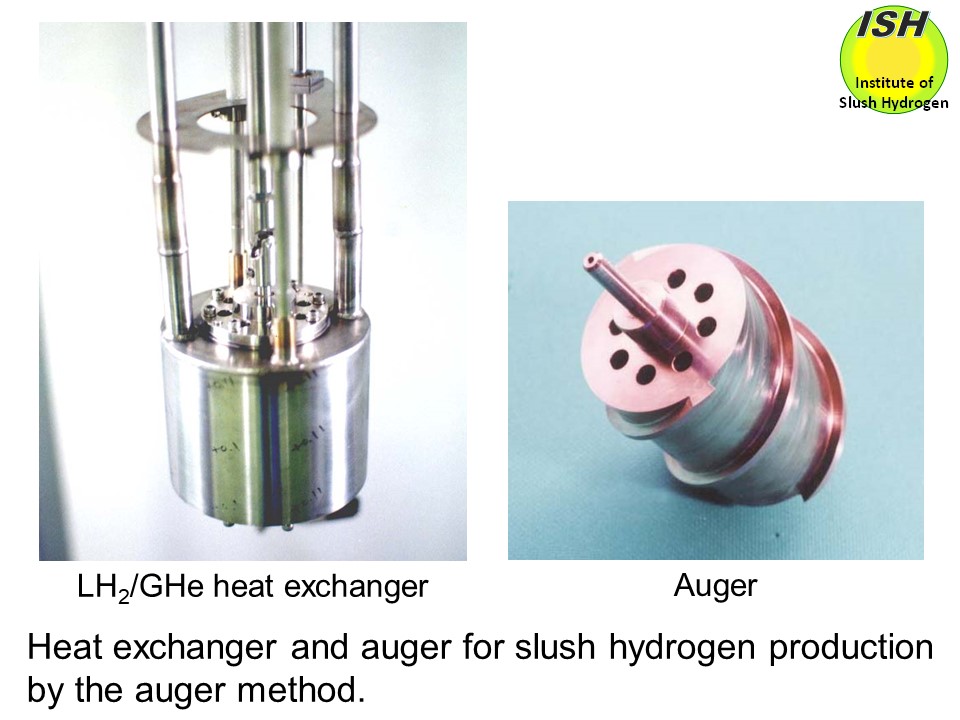
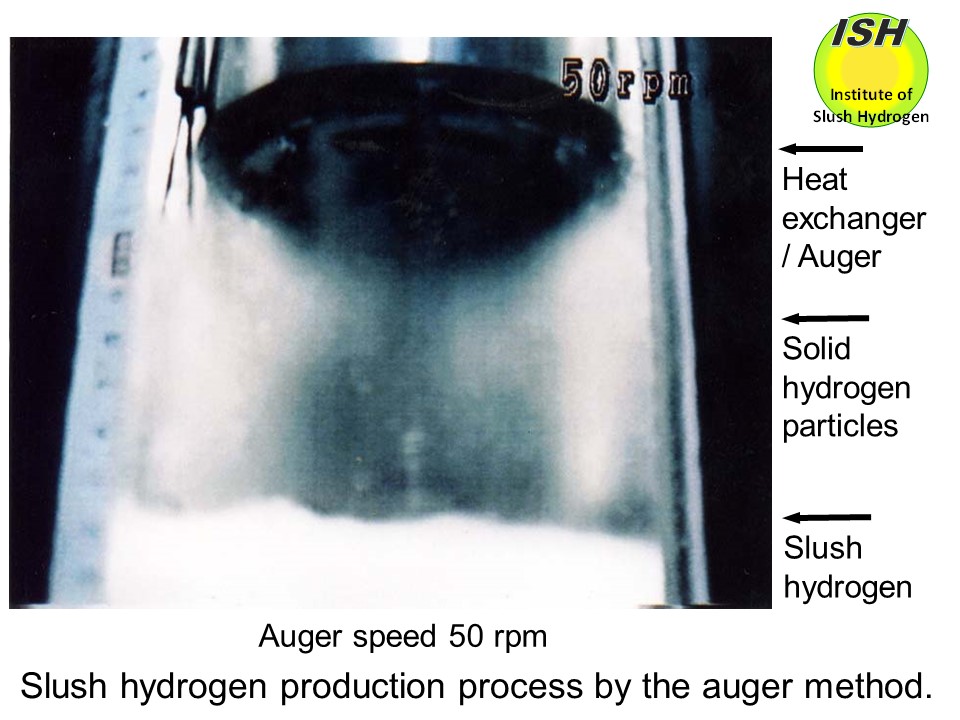
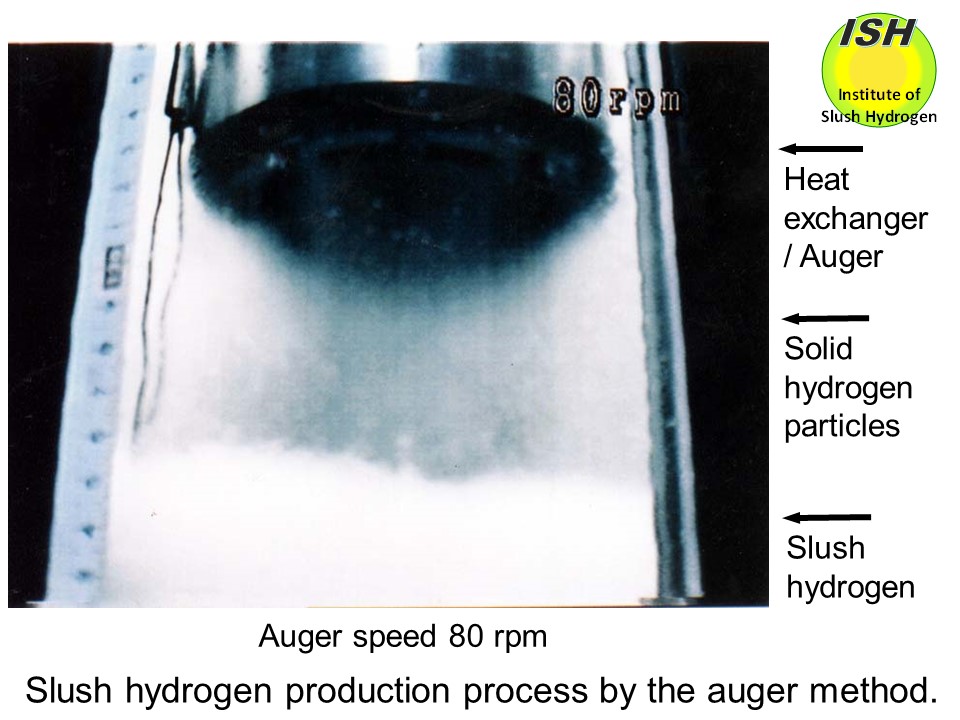
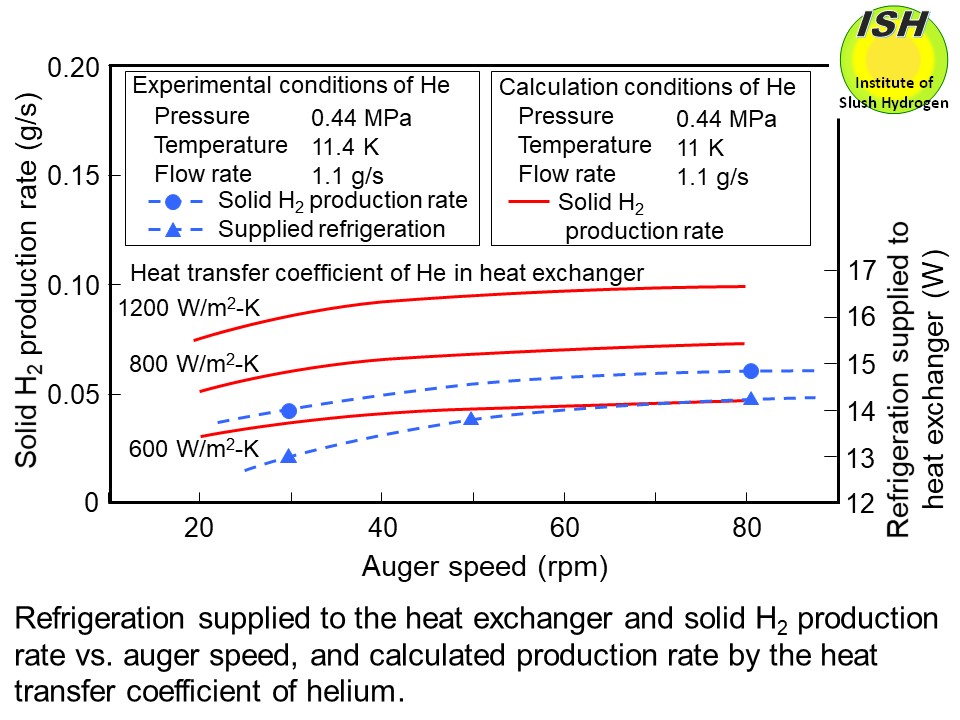