Pressure drop reduction and heat transfer deterioration of circular, triangular and square pipes
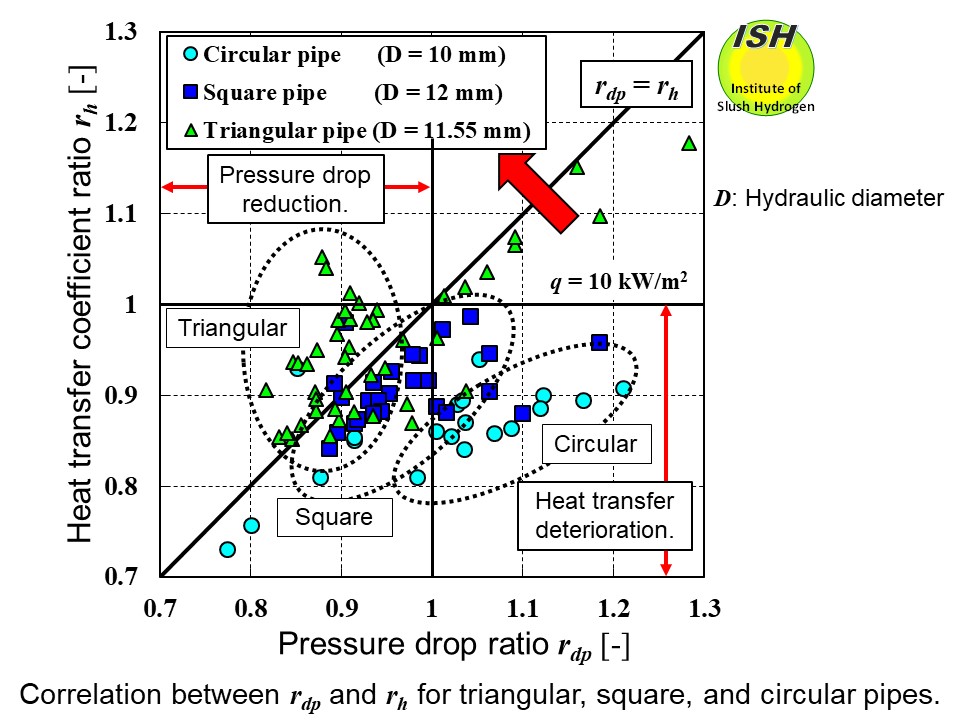
The correlation between the pressure drop ratio rdp and the heat transfer coefficient ratio rh at the same flow velocity, as experimentally obtained with respect to
triangular pipe (Type A) with sides of 20 mm (D = 11.55 mm), circular pipe with an inner diameter of 10 mm (D = 10 mm), and square pipe with sides of 12 mm (D = 12 mm), each at the same heat flux (10 kW/m2) is shown in the above figure. Pressure drop ratio is the ratio of slush nitrogen pressure drop to liquid
nitrogen pressure drop, and heat transfer coefficient ratio is the ratio
of the heat transfer coefficient for slush nitrogen to that for liquid
nitrogen. The hydraulic diameter of each pipe is about the same. About
the mechanism involved in pressure drop reduction and heat transfer deterioration,
refer to the page "Circular pipe flow and PIV".
Although the maximum pressure drop reduction and the maximum heat transfer
deterioration for a circular pipe are greater than those for triangular
and square pipes as described in "circular pipe flow" and "triangular
pipe flow", rh for the triangular pipe tends to be greater than rdp ( rh > rdp).
In order to confirm this phenomenon, the numerical analysis code (SLUSH-3D) we developed is utilized to consider the distribution of turbulent energy
k in liquid nitrogen for unheated slush nitrogen flowing through the circular
pipe (D = 15 mm) and a triangular pipe (Type A) with sides of 26 mm (D = 15 mm) having the same hydraulic diameter as for the circular pipe (refer
to "Numerical analysis of slush flow by SLUSH-3D"). These analysis
results are also illustrated in the figure below.
Even though the hydraulic diameter is the same, the influence of the turbulent
energy occurring at the apexes means that the average turbulent energy
kav is greater for the triangular pipe than for the circular pipe Accordingly,
in the comparison of the triangular pipe (Type A, D = 11.55 mm) pipe and the 10mm circular pipe as well, the average turbulent
energy of the former is greater. This suggests that the pressure drop reduction and heat transfer deterioration
effects in Type A pipe would be limited by the turbulence, and the pressure
drop and heat transfer coefficient ratios for the circular pipe would both
be lower.
In the case of circular pipe, the flow becomes pseudo-homogeneous as the
flow velocity increases, and the majority of the solid particles move toward
the pipe center region as shown at the upper left side of the figure below.
In the case of triangular pipe as well, most of the solid particles are
considered to be flowing at the pipe center region, where there is low
turbulent energy as indicated at the lower right side of the figure below. The presence in the three apexes of a substantial liquid layer having
few solid particles means that direct interference between the solid particles
and the pipe wall is lessened. As a result, pressure drop decreases in
comparison with circular pipe. As indicated at the upper right side of the figure below, due to the secondary flows of the second kind along the pipe wall near
the apex [37], heated liquid in the pipe wall vicinity is dispersed toward
the pipe center, such that the triangular pipe is considered to promote
heat transfer.
In square pipe as well, the magnitude of average turbulent energy kav, not presented here [27], is between the values for triangular and circular
pipes. Given that the amount of liquid layer at the four apexes is not
as great as in the case of triangular pipe, the influence of the liquid
layer is considered to be less in the square pipe. Accordingly, the above figure also shows a similar ordering of properties.
Given that heat transfer deterioration is normally undesirable, the selection
of pipe cross-sectional shape might depend on whether greater emphasis
is being placed on pressure drop or heat transfer in the specific design
of heat transfer piping for slush fluids.
For example, in a long-distance pipeline for the exclusive transport of
slush hydrogen, circular pipe characterized by substantial pressure drop
reduction would be suitable from the standpoint of reduced pumping power.
For refrigerant piping in a high-temperature superconducting power transmission
system, the pipe cross-section (circular or rectangular) would be important
in terms of heat transfer properties to prevent quench propagation. Meanwhile,
in the case of heat exchanger, it would be effective from a design perspective
to select triangular flow passage as a cross-sectional shape that would
limit heat transfer deterioration.
From experimental data points for the unheated triangular pipe (Type A,
B, and C) and the unheated circular pipes with inner diameters of 10 mm
and 15mm, the least squares approximation method was utilized to derive the second
correlation equation for the integrated prediction of the pipe friction
factor in both triangular and circular pipes, taking into account pressure
drop reduction.
With respect to the slush Reynolds number, the liquid nitrogen viscosity
and the apparent viscosity μSL = μL [1- (x/0.6)]-1.8 [33] were employed for triangular and circular pipes, respectively. Because
the hydraulic diameters of the triangular and circular pipes differ, a
modified slush Reynolds number was utilized, taking into account the measured
average diameter of the solid nitrogen particles s (1.36 mm) and the hydraulic diameter D. The correlation equation between the modified Reynolds number ReSL* and the pipe friction factor λfor both triangular and circular pipes is shown in the figure below.
The correlation equation is effective for design work when estimating
required pumping power for the transport of slush nitrogen.
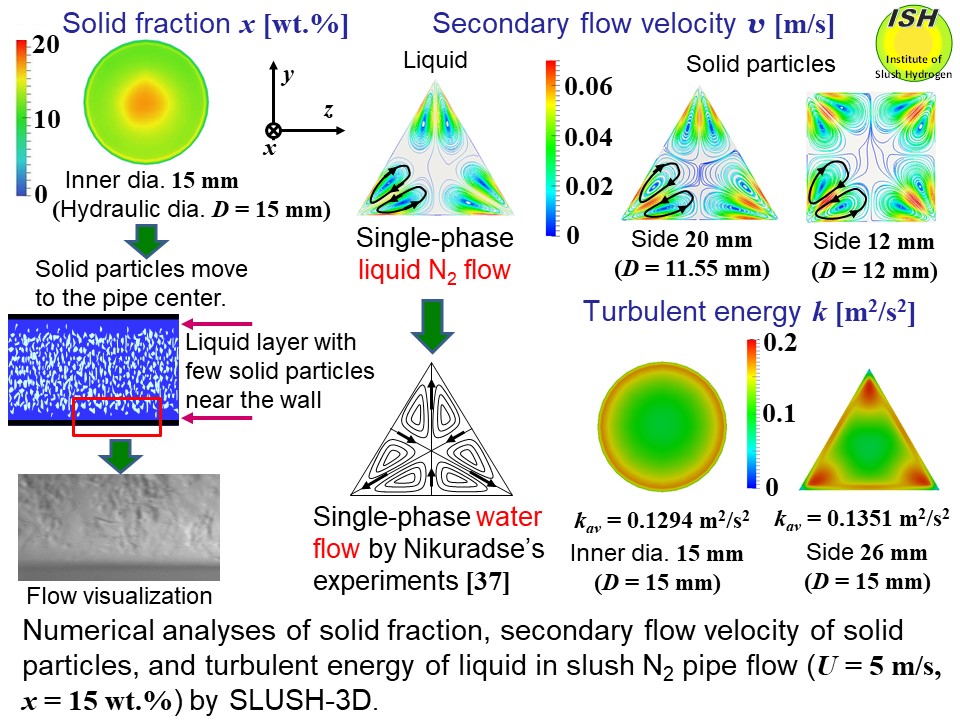
