Development of numerical code (SLUSH-3D), and flow and heat transfer characteristics of slush fluid
The purpose of the numerical analysis is to analyze three-dimensional
flow and heat transfer characteristics of slush fllow in a horizontal pipe.
Since two-dimensional numerical analyses cannot elucidate the complex phenomena
in slush flow at all, we developed the three-dimensional numerical simulation
code “SLUSH-3D”, which uses a thermally non-equilibrium two-fluid model that takes into
account the effect of melting of the solid phase on the difference in mass,
momentum and energy exchange between the solid and liquid phases to analyze
unsteady three-dimensional flow and heat transfer behavior [25, 26].
The left side of the above figure shows the calculation results of the velocity distribution of the solid
phase in flow direction for slush nitrogen at low and high pipe inlet flow
velocities. This figure also shows the velocity distribution of solid nitrogen
particles in flow direction as shown in the PIV experiments* using solid
nitrogen particles directly as the tracer (refer to the figure in "Circular
pipe flow and PIV").
The horizontal circular pipe used in the numerical analyses and slush
nitrogen experiments had an inner diameter of 15 mm. The horizontal axis
shows the solid phase flow velocity normalized for the average velocity,
and the vertical axis shows the point where the pipe’s central axis intersects
the vertical plane.
At both low and high flow velocities, the results of the numerical analysis
are in good agreement with the results of the PIV experiment*. Further,
the results of the numerical analysis of pressure drop analysis in liquid
nitrogen, which are not shown here, are in good agreement with calculated
values for pressure drop in horizontal circular pipes using the Prandtl-Karman
eq. Based on the above results, we conclude that the numerical analysis code
“SLUSH-3D” is capable of analyzing slush fluid flows to a satisfactory
degree of accuracy.
The right side of the above figure shows the solid phase velocity distribution in flow direction for slush
nitrogen and slush hydrogen flowing through a circular pipe with an inner
diameter of 15 mm at a pipe inlet flow velocity of Uin = 1.5-5.0 m/s.
In the case of slush nitrogen, as shown in the figure, at low flow velocities
(Uin = 1.5 or 2.0 m/s) the maximum flow velocity shifts to the upper portion
of the flow channel and exhibits an asymmetric distribution (heterogeneous
flow). At high flow velocities (Uin ≥ 3.0 m/s) the flow velocity distribution exhibits top-bottom symmetry
(pseudo-homogeneous flow) and approaches that of single-phase liquid nitrogen
flow as calculated separately. When the solid fraction exceeded 15 wt.%,
it was found the flow became more symmetrical (top-bottom) as flow velocity
increased. This result is in agreement with experimental findings showing
that when the inlet flow velocity was Uin = 3.6 m/s or higher, the flow became pseudo-homogeneous flow (refer to
the figure in "Circular pipe flow and PIV").
While slush hydrogen shows similar tendencies to slush nitrogen, the solid
fraction, not shown here, is more uniform at low flow velocity in slush
hydrogen than in slush nitrogen. The solid-liquid density ratio for slush
hydrogen is 1.12, while that for slush nitrogen is 1.18. This means that
the effect of gravity on the solid phase inertia is smaller, and as a result
the solid fraction at the bottom of the flow channel is smaller in slush
hydrogen than in slush nitrogen. In addition to the fact that the solid-liquid
density ratio for slush hydrogen is lower, the viscosity of liquid hydrogen
is also only 1/(11.3) that of liquid nitrogen. Therefore the drag between
the solid and liquid phases is reduced, and as a result, the velocity distribution
of the solid phase can reach a pseudo-homogenous state more easily at lower
flow velocities in slush hydrogen than in slush nitrogen.
Our analytical finding that low flow-velocity slush hydrogen achieves
a pseudo-homogenous state more easily than slush nitrogen, taken together
with our experimental result showing that a pressure drop reduction occurs
during pseudo-homogenous flow, suggests that the pressure drop reduction
may appear at a lower flow velocity in slush hydrogen than in slush nitrogen.
In other words, these experimental findings show that when the solid
fraction is the same, the pressure drop reduction effect is observed at
a lower flow velocity in slush hydrogen than in slush nitrogen [20, 26].
This validates our analytical result indicating that slush hydrogen achieves
pseudo-homogenous flow more easily than slush nitrogen. About the mechanism
involved in pressure drop reduction and heat transfer deterioration, refer
to the page "Circular pipe flow and PIV".
To elucidate the pressure drop reduction phenomenon, SLUSH-3D was utilized
for unheated slush nitrogen to consider the distribution of mass solid
fraction for a circular pipe, the distribution of secondary flow velocity
of the second kind of solid particles for an equilateral triangular pipe
[37], and the distributions of turbulent energy for a circular pipe and
an equilateral triangular pipe. The conditions of calculation were inlet
flow velocity Uin = 5 m/s, average solid fraction x = 15 wt.%, solid particle diameter of 1.3 mm, and heat flux q = 0 kW/m2.
Numerical analysis results are shown in the figure below. Here, turbulent energy k (m2/s2) is the sum of squares of the x, y, and z components of fluctuating velocity u, v, and w. The average value for the relevant pipe cross-section is kav [22, 24].
The upper left figure is the mass solid fraction distribution at the pipe cross section of a
circular pipe with an inner diameter of 15 mm, employing the kinetic theory
that considers collisions between the solid particle and the pipe wall,
and among particles. During pseudo-homogeneous flow at high flow velocity,
the phenomenon in which solid particles move toward the pipe center region
is clearly illustrated.
The upper right figures show the streamlines, flow velocities, and flow directions (arrows) associated
with secondary flow of solid particles in an equilateral triangular pipe
with sides of 20 mm and a square pipe with sides of 12 mm. While there
is hardly any secondary flow near the pipe center, two similar-sized vortices
are seen at each apex, flowing from the center to the apex, and then returning
to the center after travelling the pipe wall. Numerical analysis, not presented
here, indicates that secondary flows exist for high-velocity liquid nitrogen
and slush nitrogen flows in square and triangular pipes.
The lower right figures show the distribution of turbulent energy generating in liquid nitrogen
for a circular pipe with an inner diameter of 15 mm, and an equilateral
triangular pipe with sides of 26 mm having the same hydraulic diameter
(D = 15 mm) as for the circular pipe. Even though the hydraulic diameter
is the same, the influence of the turbulent energy generating at the apexes
means that the average turbulent energy is greater for the triangular pipe
than for the circular pipe.
The effects of the secondary flow of the second kind of solid particles
and liquid nitrogen, and the distribution of turbulent generating in liquid
nitrogen on pressure drop reduction and heat transfer deterioration are
described in "Circular, triangular, and square pipe flows".
* PIV method: The velocity of solid particles is directly measured using
the Particle Image Velocimetry method.
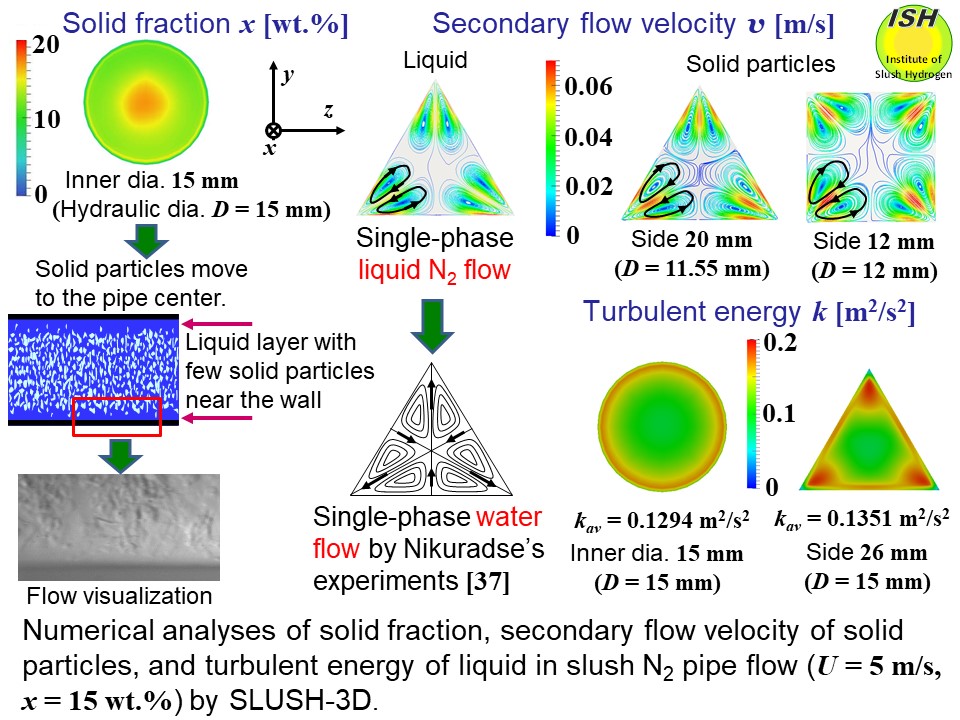